Ferro molybdenum (FeMo) is a crucial alloy used in the steel industry to impart strength, toughness, and resistance to corrosion in steel. The process of manufacturing Ferromolybdän-Pulver involves a series of complex steps and technical challenges. Jinchun, a leading metal powder manufacturer, has developed advanced techniques to overcome these challenges and ensure high-quality production of ferro molybdenum powder for industrial applications. This article explores the key technical hurdles encountered in the manufacturing of ferro molybdenum powder and the strategies employed to address them.
1. Raw Material Selection and Preprocessing
The quality of Ferromolybdän-Pulver begins with the selection of raw materials, which typically include molybdenum ore (molybdenite), molybdenum trioxide, and iron. The complexity of the raw material processing is one of the first technical challenges in the production of FeMo powder:
- Purity and Consistency: Molybdenum ore can contain impurities such as sulfur, arsenic, and other trace metals that must be removed to ensure the quality of the final product. This requires a series of purification steps, such as flotation, roasting, and leaching.
- Iron Source: The source of iron for ferro molybdenum powder must also be carefully selected to ensure that the iron content is consistent and appropriate for alloying with molybdenum. Iron scrap, ferrous oxide, or pure iron can be used, but each has different cost implications and quality outcomes.
Jinchun focuses on sourcing high-purity raw materials and using advanced preprocessing techniques to ensure the consistency and quality of the final powder.
2. Molybdenum Reduction Process
The production of ferro molybdenum involves reducing molybdenum trioxide or molybdenum oxide (MoO3) with iron to form an alloy containing molybdenum and iron. The reduction process is one of the most technically demanding stages in the production of FeMo powder:
- High Temperature Requirements: The reduction of molybdenum oxide typically takes place at temperatures between 1,100°C and 1,400°C. Achieving and maintaining these high temperatures is a significant challenge, as it requires specialized furnaces and careful temperature control.
- Reaction Control: The reduction process must be carefully controlled to avoid over-reduction, which can lead to a low yield of molybdenum in the alloy, or under-reduction, which can result in excessive impurities. Ensuring the right stoichiometry of reactants is critical for producing ferro molybdenum with the desired properties.
- Time Optimization: The reduction process must be optimized to balance time and temperature, as prolonged exposure to high temperatures can lead to the formation of unwanted compounds, while insufficient reduction time can result in an incomplete reaction.
Jinchun employs advanced high-temperature reactors and automated systems to monitor and control the reduction process, ensuring that the process remains efficient and the product quality meets industry standards.
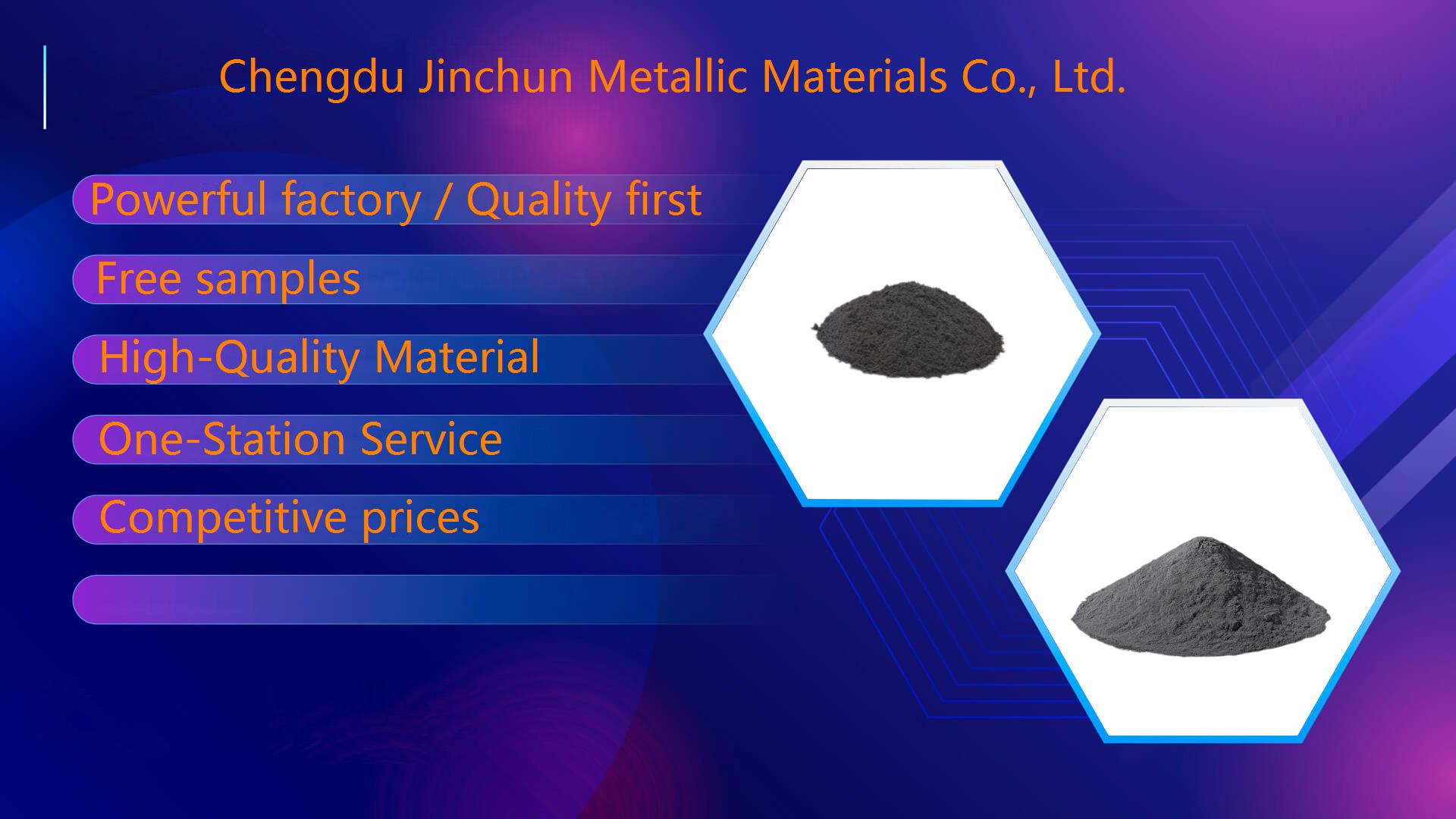
3. Cooling and Alloy Separation
Once the reduction reaction is completed, the ferro molybdenum alloy must be cooled and separated into its constituent elements. This cooling and separation process introduces several challenges:
- Cooling Rate: The cooling rate must be controlled to ensure that the alloy solidifies evenly and that the molybdenum and iron are properly blended. Rapid cooling can cause segregation or the formation of undesirable phases, while slow cooling can lead to the growth of coarse particles.
- Alloy Separation: After cooling, the ferro molybdenum alloy is typically in the form of large lumps that need to be crushed and separated into fine powder. This process must be done without losing molybdenum content or introducing impurities.
Jinchun uses controlled cooling techniques and advanced crushing methods to ensure the uniformity of the alloy and minimize losses during the separation process.
4. Powderization and Particle Size Control
The next step in the manufacturing of ferro molybdenum powder is to reduce the alloy into a fine powder. The powderization process is critical, as the particle size of the powder directly influences its performance in applications such as steel production:
- Mechanical Milling: The alloy is typically crushed or ground into powder using mechanical milling techniques such as ball milling or hammer milling. Achieving a consistent particle size distribution is challenging, as uneven grinding can lead to a mix of fine and coarse particles, which affect the powder’s reactivity and performance.
- Size Distribution: Ferro molybdenum powder needs to have a narrow particle size distribution to ensure uniform dispersion in steel melts. Inconsistent particle size can lead to uneven alloying in the steel, affecting the material’s mechanical properties.
- Powder Flowability: The powder must also have good flowability to be easily transported and mixed with other ingredients in the steelmaking process. Poor flowability can lead to inconsistent alloying and product defects.
To meet these challenges, Jinchun uses state-of-the-art grinding equipment and advanced screening methods to control particle size and ensure uniformity in the final powder.
5. Controlling Impurity Levels
The presence of impurities in ferro molybdenum powder can significantly degrade the quality of the alloy and affect the performance of the steel made from it. Controlling the impurity levels is a critical challenge in the manufacturing process:
- Iron Contamination: Even though iron is an essential component of ferro molybdenum, excess iron can be detrimental to the properties of the alloy. Over-reduction or poor separation during the cooling process can result in high iron content, affecting the powder’s reactivity and overall performance.
- Residual Carbon and Sulfur: Carbon and sulfur are typically considered impurities in ferro molybdenum powder. Excess carbon can lead to carbide formation in steel, while sulfur can affect the steel’s ductility and weldability.
- Trace Elements: Other trace elements, such as arsenic, lead, or phosphorus, must be kept at low levels to prevent defects in the final product.
To ensure the purity of the ferro molybdenum powder, Jinchun employs advanced refining techniques, including high-temperature vacuum processing and precision filtration, to minimize contamination from impurities.
6. Quality Control and Testing
Maintaining consistent quality is vital throughout the production of ferro molybdenum powder. Several quality control measures are put in place to monitor the production process and ensure that the final product meets the required specifications:
- Chemical Composition Analysis: Regular chemical analysis is performed using techniques such as X-ray fluorescence (XRF) or inductively coupled plasma (ICP) to monitor the molybdenum and iron content, as well as impurity levels.
- Partikelgrößenverteilung: Particle size is carefully measured using methods like laser diffraction or sieve analysis to ensure that the powder meets the required specifications for steel alloying.
- Flowability and Bulk Density: The powder’s flowability and bulk density are tested to ensure it is suitable for steelmaking processes.
Jinchun maintains a strict quality assurance program, performing tests at every stage of production to ensure that the ferro molybdenum powder meets industry standards and customer specifications.
7. Packaging and Distribution
The final step in the production of ferro molybdenum powder involves packaging and distribution. The powder must be carefully handled to prevent contamination or oxidation, and it needs to be packaged in a manner that maintains its quality during storage and transportation:
- Moisture Control: Ferro molybdenum powder is sensitive to moisture, which can lead to oxidation and degradation of quality. Proper moisture control during packaging is essential to prevent deterioration during transit.
- Packaging Materials: The powder is typically packaged in sealed, moisture-proof containers to maintain its integrity. The packaging must be durable enough to withstand handling during transportation without compromising the quality of the powder.
Jinchun uses specialized packaging techniques to ensure that the ferro molybdenum powder reaches customers in optimal condition, ready for use in steel production.
Jinchun remains committed to overcoming the technical challenges in the manufacturing of Ferromolybdän-Pulver by using advanced technologies and strict quality control measures. Through continuous innovation and precision, Jinchun ensures that the ferro molybdenum powder produced meets the highest standards of quality, ensuring superior performance in steel manufacturing processes.